Fürstenwalde, July 16, 2024
On her summer tour this year, Federal Building Minister Klara Geywitz visited the modular construction factory in Fürstenwalde on 15 July 2024. A joint venture between the companies Capital Bay and Daiwa House Modular Europe acquired the site of the former steel construction company Reuther STC in 2022 and converted the existing halls so that the production of building modules, which are primarily intended for residential construction, can take place. Capital Bay CEO George Salden and Andreas Göbel, Head of Acquisition at Daiwa House Modular Europe, gave the Minister a tour of the production facilities.
George Salden pointed out the advantages of building with prefabricated building modules: ‘With the high degree of prefabrication of the modules in the factory, we can reduce the construction time by 50 per cent. This is because the modules are simply stacked on top of each other on the construction site and, as quality control is already carried out in the factory, there are no lengthy reworking of construction defects’. Salden goes on to emphasise:
‘The highlight, however, is the sustainability of the modules. With our modules, we offer a recyclable product and thus turn the property into a mobile asset. This is because we offer a take-back guarantee with a refund. This means that at the end of a building's utilisation cycle, we unstack the modules, refurbish them in the factory and reuse them for the construction of a new building at a different location. In this way, our modular construction saves 50 per cent of CO2 compared to traditional construction methods.’
George Salden, CEO Capital Bay
Salden still sees a need for improvement in legislation: ‘In order to build affordable housing, we need industrialised modular construction. However, we are in a contradictory situation in terms of authorisation: modular buildings are considered special buildings and are subject to an even more complex approval process than is already the case in Germany. In addition, 16 state building regulations apply in Germany and in some cases there are even special municipal requirements. It's as if a car has to be specially authorised in every city it is allowed to drive through.’
I see great potential in serial and modular construction for Germany, particularly in the area of affordable housing. That's why we need to take this construction method out of its niche and make it more widespread. With the planned harmonised type approval for the state building regulations, which is to be introduced as part of the acceleration pact, the approval processes for construction projects can be significantly simplified. We have also launched a funding programme with a sum of 2 billion euros for the climate-friendly construction of new homes in the low-price segment. This is also an important prerequisite. This can give a boost to modular construction.
Federal Building Minister Klara Geywitz
Around 230 employees currently work in production in Fürstenwalde. ‘With the planned expansion of production capacity, this number will rise to around 1,500. In this final expansion stage of the plant, up to 30,000 modules will roll off the production line every year,’ says Salden.
As part of an initial contract, around 3,000 modules will be produced in Fürstenwalde for a Gewobag residential project. In the Berlin district of Lichtenberg at Landsberger Allee 341-343, the state-owned housing association is constructing four buildings with more than 1,400 flats - the largest modular housing project in Europe. Construction will take around three years.
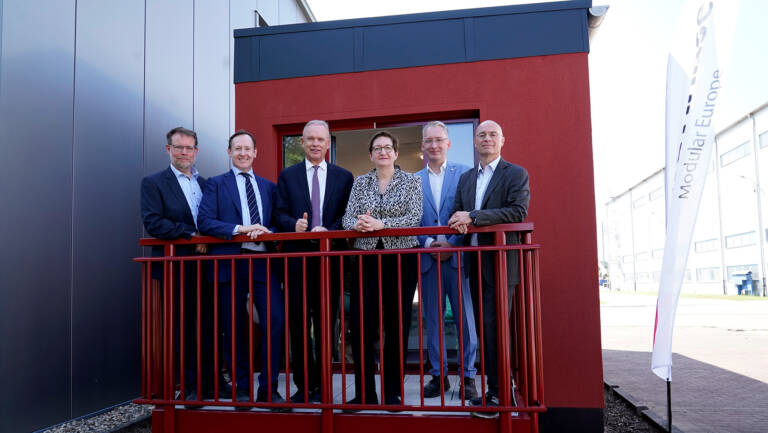
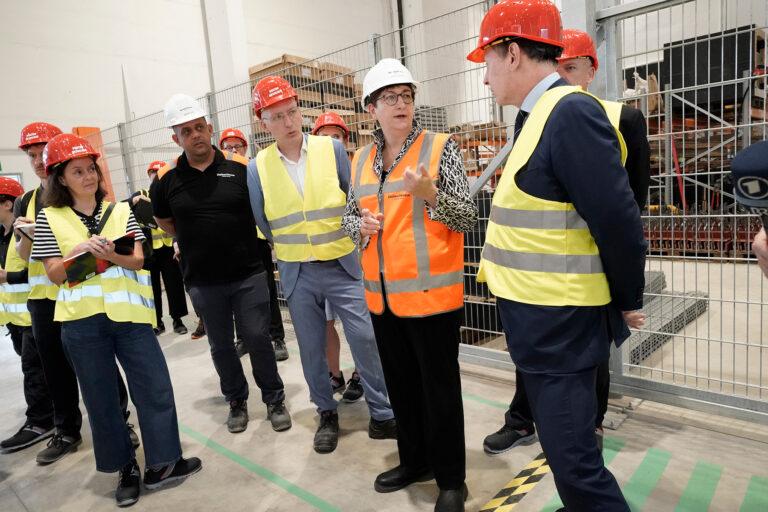
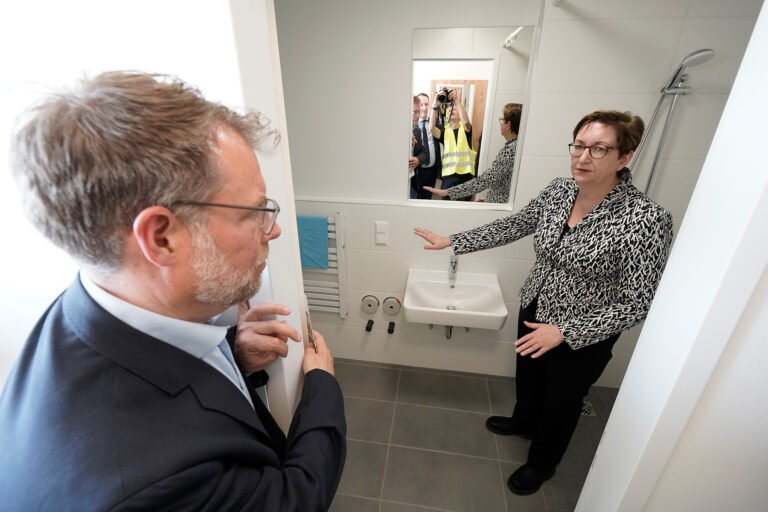
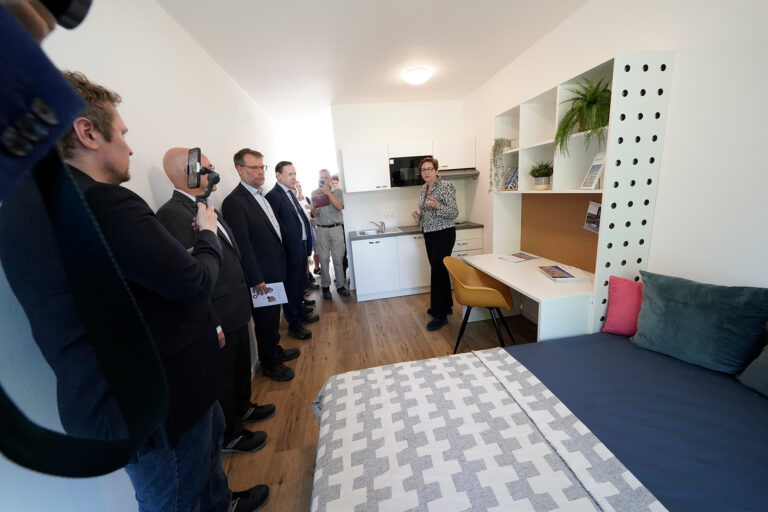